납땜
Soldering
솔더링(Soldering, 미국: /ˈsədɪŋrɪŋ/; 영국: /ˈsəldʊrɒ/)은 솔더(solder)라고 불리는 필러 금속을 사용하여 두 금속 표면을 함께 접합하는 공정입니다.솔더링 공정은 접합될 표면을 가열하고 땜납을 녹이는 과정을 포함하며, 땜납은 냉각 및 응고되어 견고하고 내구성 있는 접합부를 형성합니다.
납땜은 인쇄 회로 기판(PCB) 및 기타 전자 부품의 제조 및 수리를 위해 전자 산업에서 일반적으로 사용됩니다.그것은 또한 배관과 금속 가공뿐만 아니라 보석과 다른 장식품의 제조에도 사용됩니다.
공정에 사용되는 솔더는 다양한 용도에 사용되는 합금과 함께 조성이 다양할 수 있습니다.일반적인 솔더 합금으로는 주석-납, 주석-은 및 주석-구리 등이 있습니다.무연 솔더는 또한 최근 납 사용과 관련된 건강 및 환경 문제로 인해 더욱 널리 사용되고 있습니다.
사용되는 솔더의 종류 이외에도, 가열의 온도와 방법 또한 솔더링 공정에서 중요한 역할을 합니다.땜납 종류에 따라 녹는 온도가 달라야 하며, 접합되는 재료가 손상되거나 약한 접합부가 생기지 않도록 가열을 신중하게 제어해야 합니다.
납땜에 사용되는 가열 방법에는 납땜용 다리미, 횃불, 열풍총 등 여러 가지가 있습니다.각각의 방법은 각각의 장점과 단점이 있으며, 방법의 선택은 응용 프로그램과 결합되는 재료에 따라 달라집니다.
납땜은 많은 산업과 취미에 중요한 기술이며, 좋은 결과를 얻기 위해서는 기술적 지식과 실무 경험의 결합이 필요합니다.
오리진스

납땜이 메소포타미아에서 [1]일찍이 5,000년 전에 사용되었다는 증거가 있습니다.납땜과 납땜은 아마도 [2]기원전 4000년 이전에 금속 세공의 역사에서 아주 초기에 시작된 것으로 생각됩니다.기원전 3000년 수메르의 칼들은 단단한 납땜을 사용하여 조립되었습니다.
납땜은 역사적으로 보석, 요리 도구, 스테인드 글라스 조립 및 기타 용도로 사용되었습니다.
적용들
납땜은 배관, 전자제품, 금속 세공에서 번쩍임에서 보석, 악기에 이르기까지 사용됩니다.
납땜은 배관 시스템의 구리 파이프와 음식 캔, 지붕 점멸, 배수구 및 자동차 방열기와 같은 판금 물체의 접합부 사이에 비교적 영구적이지만 가역적인 연결을 제공합니다.
보석 부품, 공작 기계 및 일부 냉동 및 배관 부품은 종종 고온의 은 납땜 공정에 의해 조립 및 수리됩니다.작은 기계 부품도 납땜되거나 납땜되는 경우가 많습니다.납땜은 또한 스테인드 글라스 작업에서 납과 동박을 결합하는 데 사용됩니다.
전자 납땜은 전기 배선을 장치에 연결하고 전자 부품을 인쇄 회로 기판에 연결합니다.전자 연결부는 납땜용 다리미로 손으로 납땜할 수 있습니다.웨이브 솔더링이나 오븐 사용과 같은 자동화된 방법으로 복잡한 회로 기판에 많은 접합부를 한 번의 작업으로 만들 수 있어 전자 장치의 생산 비용을 크게 절감할 수 있습니다.
악기, 특히 금관악기와 목관악기는 납땜과 납땜의 조합을 조립에 사용합니다.황동 몸체는 납땜을 함께 하는 경우가 많고, 키워크와 교정기는 납땜을 하는 경우가 가장 많습니다.
납땜성
기판의 납땜성은 해당 재료에 납땜 접합을 쉽게 만들 수 있는 척도입니다.
어떤 금속들은 다른 금속들보다 납땜하기가 더 쉽습니다.구리, 아연, 황동, 은 그리고 금은 쉽습니다.철, 연강, 니켈이 그 다음으로 어려움에 처해 있습니다.얇고 강한 산화막으로 인해 스테인리스 스틸과 일부 알루미늄 합금은 납땜이 더욱 어렵습니다.티타늄, 마그네슘, 주철, 일부 고탄소강, 세라믹 및 흑연을 납땜할 수 있지만 탄화물 접합과 유사한 공정을 포함합니다. 먼저 계면 결합을 유도하는 적합한 금속 원소로 도금됩니다.
솔더스
납땜 필러 재료는 다양한 용도로 다양한 합금으로 제공됩니다.전자 부품 조립에서 63% 주석과 37% 납(또는 융점이 거의 동일한 60/40)을 가진 공융 합금이 선택된 합금입니다.다른 합금들은 배관, 기계적 조립 및 기타 용도로 사용됩니다.연납의 예로는 일반 용도의 주석 납, 알루미늄 접합용 주석 아연, 상온보다 높은 강도의 납 은, 고온 강도의 카드뮴 은, 알루미늄과 내식성의 아연 알루미늄, 전자 제품의 주석 은 및 주석 비스무트 등이 있습니다.
공융 제형은 납땜에 적용할 때 장점이 있습니다: 액체와 고체의 온도가 같아서 플라스틱 상이 없고 용융점이 가장 낮습니다.용융점이 가장 낮으면 납땜 시 전자 부품에 가해지는 열 스트레스를 최소화할 수 있습니다.또한 플라스틱 단계가 없기 때문에 솔더가 가열됨에 따라 더 빨리 젖고, 솔더가 냉각됨에 따라 더 빠르게 설정할 수 있습니다.비-유능 제형은 액체 및 고체 온도를 통해 온도가 떨어질 때 가만히 있어야 합니다.플라스틱 단계에서 움직일 경우 균열이 발생하여 조인트가 신뢰할 수 없습니다.
주석과 납을 기반으로 한 일반적인 솔더 제형은 아래에 나열되어 있습니다.분율은 주석의 비율을 먼저 표시한 다음 납의 비율을 총 100%로 나타냅니다.
- 63/37: 183 °C (361 °F)에서 녹습니다 (유능성: 범위가 아닌 한 점에서 녹는 유일한 혼합물)
- 60/40: 183~190°C(361~374°F) 사이에서 녹습니다.
- 50/50: 183~215°C(361~419°F) 사이에서 녹습니다.
환경적인 이유와 유럽 RoHS(Restrict of Hazardous Substances Directive)와 같은 규제 도입으로 인해 무연 솔더가 더욱 널리 사용되고 있습니다.또한 (어린 아이들이 물건을 입에 넣기 쉽기 때문에) 어린 아이들이 접촉할 수 있는 모든 장소 또는 비와 다른 강수량이 납을 지하수에 씻을 수 있는 야외용으로 사용할 것을 권장합니다.불행히도 일반적인 무연 솔더는 공융 제형이 아니며, 약 220°[3]C(428°F)에서 용융되므로 안정적인 조인트를 만드는 것이 더욱 어렵습니다.
다른 일반적인 납땜은 저온 제형(종종 비스무트를 포함함)을 포함하는데, 이는 종종 이전 납땜된 결합물을 납땜하지 않고 결합하는 데 사용됩니다.및 고온 제제(보통 은 함유)는 고온 작업 또는 후속 작업 중에 팔리지 않아야 하는 품목의 첫 번째 조립에 사용됩니다.은을 다른 금속과 합금화하면 융점, 접착력 및 습윤 특성, 인장강도 등이 변화합니다.모든 브레이징 합금 중에서 은 납땜은 가장 큰 강도와 가장 넓은 [4]용도를 가지고 있습니다.특수 합금은 강도, 알루미늄 납땜 능력, 전기 전도성 및 내식성 향상과 같은 [5]특성으로 사용할 수 있습니다.
납땜 대 납땜

납땜에는 세 가지 형태가 있으며, 각각의 형태는 점진적으로 더 높은 온도를 필요로 하며 점점 더 강한 조인트 강도를 생성합니다.
납땜의 종류별 충전재 금속의 합금을 조정하여 충전재의 용융 온도를 조정할 수 있습니다.솔더링은 접합부의 작업물 표면에 충전재 금속이 직접 결합하여 전기 전도성과 가스 및 액체에 [7]모두 밀착되는 결합을 형성한다는 점에서 접착과는 크게 다릅니다.
연성 솔더링은 충전재 금속의 융점이 약 400°C([8]752°F) 미만인 것이 특징인 반면, 은 솔더링과 브레이징은 고온을 사용하므로 충전재의 융점을 달성하기 위해 일반적으로 화염 또는 탄소 아크 토치가 필요합니다.연질 솔더 필러 금속은 일반적으로 액체 온도가 350 °C(662 °F) 미만인 합금(종종 납 함유)입니다.
이러한 솔더링 공정에서는 접합되는 부분에 열이 가해져 땜납이 용융되어 웨팅(wetting)이라 불리는 표면 합금화 공정으로 작업물에 접합하게 됩니다.연선에서 땜납은 '위킹'이라고 불리는 과정에서 모세관 작용에 의해 연선 사이의 전선으로 인입됩니다.모세관 작용은 공작물이 매우 가까이 있거나 맞닿을 때도 발생합니다.접합부의 인장 강도는 사용되는 필러 금속에 따라 다릅니다. 전기 납땜의 경우 추가된 납땜에서 인장 강도가 거의 나오지 않으므로 접합부에 기계적 강도를 제공하기 위해 납땜 전에 와이어를 함께 꼬거나 접는 것이 좋습니다.양호한 솔더 조인트는 전기 전도성, 수분 및 가스 기밀 조인트를 생성합니다.
솔더의 종류는 각각 장단점을 제공합니다.연납은 그 주성분인 연납 때문에 그렇게 불립니다.연질 납땜은 가장 낮은 온도를 사용하지만(따라서 열응력 구성요소가 가장 적음) 강한 조인트를 만들지 않으며 기계적 하중을 받는 용도에는 적합하지 않습니다.강도가 떨어져 결국 녹기 때문에 고온 적용에도 부적합합니다.은 납땜은 보석상, 기계공 및 일부 배관 작업에 사용되는 것처럼 토치나 기타 고온 소스를 사용해야 하며 연 납땜보다 훨씬 강력합니다.브레이징은 용접되지 않은 접합부 중 가장 강력한 접합부를 제공하지만 필러 금속을 녹이기 위해서는 가장 뜨거운 온도가 필요하므로 고온 작업에서 생성되는 밝은 빛으로부터 눈을 보호하기 위해 토치 또는 기타 고온 소스와 검게 칠한 고글이 필요합니다.주철물, 연철 가구 등을 수리하는 데 자주 사용됩니다.
납땜 작업은 수공구로, 한 번에 하나씩 접합하거나 생산 라인에서 일괄적으로 수행할 수 있습니다.손 솔더링은 일반적으로 인두, 솔더링 건 또는 토치, 또는 경우에 따라 열풍 연필을 사용하여 수행됩니다.판금 작업은 전통적으로 불꽃에 의해 직접 가열된 "납땜 구리"로 이루어졌으며, 납땜 구리 덩어리에 충분한 열이 저장되어 접합부를 완성할 수 있었습니다. 가스 횃불(예: 부탄 또는 프로판) 또는 전기로 가열된 납땜 다리미가 더 편리합니다.모든 납땜 접합부에는 접합할 금속 부품의 세척, 접합부 장착, 부품 가열, 플럭스 도포, 충전재 도포, 열 제거, 충전재 금속이 완전히 응고될 때까지 어셈블리를 정지 상태로 유지하는 동일한 요소가 필요합니다.사용되는 플럭스 소재의 특성과 용도에 따라, 조인트가 냉각된 후에 조인트의 세척이 필요할 수 있습니다.
각 솔더 합금은 특정 용도에 가장 적합한 특성을 가지고 있으며, 특히 강도와 전도성이 있으며, 솔더와 합금의 종류별로 용융 온도가 다릅니다.실버 솔더란 사용되는 솔더의 종류를 의미합니다.일부 연질 납땜기는 은도금 제품을 납땜하는 데 사용되는 "은을 함유한" 합금입니다.납을 사용하는 납땜기는 납이 금속을 용해시켜 변형시키기 때문에 귀금속에 사용해서는 안 됩니다.
납땜과 브레이징의 구분은 필러 합금의 용융 온도를 기준으로 합니다.일반적으로 납땜과 브레이징 사이의 실질적인 구분으로 450°C의 온도를 사용합니다.다른 방법들은 일반적으로 필러 금속을 용해하기 위해 더 높은 온도의 토치 또는 용해로를 필요로 하는 반면, 연질 납땜은 가열된 철을 사용하여 수행될 수 있습니다.
납땜용 철은 단단한 납땜이나 납땜을 하기에 충분한 온도를 얻을 수 없기 때문에 일반적으로 다른 장비가 필요합니다.납계 연질 솔더보다 강한 은납보다 브레이징 필러 메탈이 더 강합니다.브레이징 솔더는 주로 강도를 위해 제조되며, 은 솔더는 귀금속을 보호하기 위해 보석상에 의해 사용되며, 기계 및 냉동 기술자는 인장 강도를 위해 사용되지만 브레이징보다 용융 온도가 낮습니다.소프트 솔더의 주요 이점은 낮은 온도(전자 부품 및 절연에 대한 열 손상 방지)입니다.
접합부는 공작물보다 용융온도가 낮은 금속을 사용하여 제작되기 때문에 주변 온도가 충전재 금속의 용융점에 가까워질수록 접합부가 약해질 수 있습니다.이러한 이유로 높은 온도 공정에서는 높은 온도에서 효과적인 조인트가 생성됩니다.브레이징 접합부는 높은 [10]온도에서도 연결된 [9]부품만큼 강하거나 거의 강할 수 있습니다.
은납땜
"하드 솔더링" 또는 "실버 솔더링"은 금, 은, 황동, 구리와 같은 귀금속과 반귀금속을 결합하는 데 사용됩니다.솔더는 일반적으로 접합부의 강도가 아닌 용융 온도와 관련하여 용이하거나 중간 또는 단단하다고 설명됩니다.은을 56% 함유하고 있으며 녹는점은 618°C(1,145°F)입니다.초경질 솔더는 80% 은을 가지며 740 °C(1,370 °F)에서 녹습니다.여러 개의 접합부가 필요한 경우, 보석상은 경질 또는 초경질 납땜으로 시작하여 나중에 접합부를 위해 저온 납땜으로 전환합니다.
은납은 주변 금속에 어느 정도 흡수되어 접합되는 금속보다 실제로 더 강한 접합부가 형성됩니다.은납은 보통 충전재로 사용할 수 없고 틈새를 메우지 않기 때문에 접합되는 금속은 완벽한 플러시(flush)여야 합니다.
납땜과 납땜의 또 다른 차이점은 납땜이 어떻게 적용되는지입니다.브레이징(brazing)에서는 일반적으로 가열된 상태에서 조인트에 접촉되는 로드를 사용합니다.은 납땜으로, 가열하기 전에 금속 위에 작은 땜납 와이어 조각들이 놓여집니다.금속과 솔더를 깨끗하게 유지하고 솔더가 녹기 전에 움직이지 못하도록 방지하기 위해 종종 붕산과 변성 알코올로 만들어진 플럭스가 사용됩니다.
은납이 녹으면 열이 가장 큰 부위로 흘러가는 경향이 있습니다.보석상들은 횃불을 들고 납땜을 이끌면 납땜이 움직이는 방향을 어느 정도 조절할 수 있습니다. 심지어 납땜은 솔기를 따라 똑바로 올라가기도 합니다.
기계 및 알루미늄 납땜
주로 아연 합금을 포함한 여러 솔더 재료는 알루미늄 금속과 합금을 납땜하는 데 사용되며 강철과 아연은 덜 사용됩니다.이 기계적 납땜은 접합부의 기계적 특성이 상당히 우수하고 해당 재료의 구조 수리에 사용할 수 있다는 점에서 저온 브레이징 작업과 유사합니다.
미국 용접 협회는 브레이징을 융점이 450°C(842°F) 이상인 필러 금속을 사용하는 것으로 정의합니다. 또는 미국에서는 전통적인 정의에 따라 800°F(427°C) 이상인 필러 금속을 사용하는 것으로 정의합니다.알루미늄 납땜 합금의 용융 온도는 일반적으로 약 730°F([11]388°C)입니다.이 솔더링/브레이징 작업은 프로판 토치 [12]열원을 사용할 수 있습니다.
이러한 재료는 흔히 "알루미늄 용접"이라고 광고하지만, 이 공정은 기본 금속을 녹이는 것이 아니므로 용접이 제대로 되지 않습니다.
미국 군사 표준 또는 MIL-SPEC 규격 MIL-R-4208은 이러한 아연 기반 브레이징/납땜 [13]합금에 대한 하나의 표준을 정의합니다.이 [12][14][15]규격을 충족하는 제품이 많습니다.또는 매우 유사한 성능 [11]기준을 제공합니다.
플럭스
플럭스의 목적은 솔더링 공정을 용이하게 하는 것입니다.성공적인 솔더 조인트의 장애물 중 하나는 조인트 부위의 불순물(예: 더러움, 오일 또는 산화)입니다.불순물은 기계적 세척 또는 화학적 방법으로 제거할 수 있지만 필러 금속(솔더)을 녹이는 데 필요한 온도가 높아지면 작업물(및 솔더)이 다시 산화됩니다.이러한 효과는 납땜 온도가 높아짐에 따라 가속화되며 솔더가 작업물에 결합하는 것을 완전히 방지할 수 있습니다.초기 형태의 플럭스 중 하나는 납땜 과정에서 산화를 방지하고 환원제 역할을 하는 숯이었습니다.일부 플럭스는 단순한 산화 방지를 넘어 화학적 세정(부식)의 형태를 제공합니다.납땜 [16]공정에서도 많은 플럭스가 습윤제로 작용하여 용융된 땜납의 표면장력을 감소시키고, 이를 유동시켜 작업물을 더 쉽게 적십니다.
여러 해 동안, 전자제품(소프트 솔더링)에 사용되는 가장 일반적인 플럭스 유형은 소나무에서 추출한 로진을 사용하는 로진 기반이었습니다.정상 온도에서는 부식성이 없고 전도성이 없지만 납땜 온도가 올라가면 약간 반응성(부식성)이 된다는 점에서 거의 이상적이었습니다.배관 및 자동차 분야에서는 일반적으로 산 기반(염산) 플럭스를 사용하여 조인트를 상당히 적극적으로 청소합니다.이러한 플럭스는 전자 장치에 사용할 수 없습니다. 왜냐하면 잔류물이 전도성을 띠어 의도하지 않은 전기적 연결을 초래하고 결국 작은 직경의 와이어를 용해시키기 때문입니다.시트르산은 구리와 전자제품에 유용한 수용성 산형 플럭스이지만 나중에 씻어내야 합니다.
연납 용 플럭스는 현재 세 가지 기본 제형으로 제공됩니다.
- 수용성 플럭스 – 납땜 후 물로 제거할 수 있는 높은 활성 플럭스(제거에 VOC가 필요 없음)
- 청결하지 않은 플럭스 – 비도전성 및 부식성 [7]잔류물로 인해 "제거"할 필요가 없을 정도로 가볍습니다.이러한 플럭스는 땜납 작업 후 남은 잔여물이 비전도성이기 때문에 전기적 단락을 일으키지 않으며, 그럼에도 불구하고 눈에 잘 띄는 흰색 잔여물을 남기기 때문에 "결함 없음"이라고 불립니다.육안 검사, 테스트 지점 접근 또는 습하고 끈적이거나 과도한 잔류물이 다른 영역으로 퍼질 수 있는 경우 IPC-610에서 정의한 대로 세 가지 등급의 PCB 모두에 클린 플럭스 잔류물이 허용되지 않습니다.커넥터 접합 표면에도 플럭스 잔류물이 없어야 합니다.청정하지 않은 잔여물의 지문은 3등급[18] 결함입니다.
- 전통적인 로진 플럭스 – 비활성화(R), 약간 활성화(RMA) 및 활성화(RA) 제형으로 제공됩니다.RA 및 RMA 플럭스에는 활성화제(일반적으로 산)와 결합된 로진이 포함되어 있으며, 이는 기존 산화물을 제거함으로써 적용되는 금속의 젖음성을 증가시킵니다.RA flux 사용으로 인한 잔여물은 부식성이 있으므로 세척해야 합니다.RMA 플럭스는 부식성이 적은 잔류물을 생성하도록 공식화되므로 세척은 일반적으로 선호되지만 선택 사항이 됩니다.R 플럭스는 여전히 활성도가 낮고 부식성도 낮습니다.
플럭스 성능은 최상의 결과를 얻기 위해 신중하게 평가되어야 합니다. 매우 가벼운 '깨끗하지 않은' 플럭스는 생산 장비에서는 완벽하게 허용될 수 있지만, 보다 가변적인 핸드 솔더링 작업에는 적절한 성능을 제공하지 못합니다.
난방방식
다양한 유형의 납땜 도구는 특정 용도에 맞게 제작됩니다.필요한 열은 연료를 연소하거나 전기로 작동하는 발열체에서 발생하거나 납땜할 물품에 전류를 통과시켜 발생할 수 있습니다.납땜을 위한 또 다른 방법은 납땜 대상물의 접합부 위치에 납땜과 플럭스를 배치한 후, 납땜을 녹이기 위해 오븐에서 전체 물체를 가열하는 것입니다. 토스터 오븐과 휴대용 적외선 조명은 취미주의자들에 의해 훨씬 작은 규모로 생산 납땜 과정을 복제하기 위해 사용되어 왔습니다.납땜의 세 번째 방법은 부품(플럭스가 있는)을 액체 납땜의 작은 가열된 철 컵에 담근 납땜 냄비 또는 액체 납땜 욕조의 펌프가 부품을 빠르게 통과시키는 높은 "파도"를 생성하는 납땜 냄비를 사용하는 것입니다.웨이브 솔더링은 표면 장력을 사용하여 솔더가 플럭스 코팅된 인쇄 배선 기판/인쇄 회로 기판의 구리 라인 사이의 절연 간극을 메우는 것을 방지합니다.
전기 납땜용 철은 구리로 만든 작업 팁과 접촉하는 "철"(금속 덩어리, 보통 구리)과 접촉하는 발열체로 구성된 손 납땜용으로 널리 사용됩니다.보통, 납땜용 다리미에는 무딘 것부터 아주 미세한 것까지 다양한 팁이 장착될 수 있습니다. 납땜용 다리미는 납땜용이 아니라 열간 절단용 플라스틱의 끌 헤드에 이르기까지 말입니다.일반 구리 팁은 핫 솔더에서 부식/용해될 수 있으며, 이를 방지하기 위해 순철로 도금될 수 있습니다.가장 간단한 다리미에는 온도 조절 기능이 없습니다.작은 다리미는 금속 섀시에 납땜할 때 급속하게 냉각되는 반면, 큰 다리미는 인쇄 회로 기판(PCB) 및 이와 유사한 세공 작업에 너무 번거로운 팁을 가지고 있습니다.25와트 철로는 대형 전기 커넥터, 접합 구리 지붕 플래시, 대형 스테인드 글라스 납 등에 충분한 열을 공급할 수 없습니다.반면에, 100와트 다리미는 PCB에 너무 많은 열을 제공할 수 있습니다.온도가 조절되는 다리미는 전력이 비축되어 있고 광범위한 작업에 걸쳐 온도를 유지할 수 있습니다.
납땜 건은 큰 단면 1회전 변압기를 사용하여 큰 교류 전류를 통과시킴으로써 작은 단면의 구리 팁을 매우 빠르게 가열하고, 구리 팁은 다른 납땜 아이언과 같이 열을 부품에 전달합니다.납땜 건은 변압기가 내장되어 있기 때문에 동일한 전력 등급의 발열체 납땜 인두보다 더 크고 더 무거울 것입니다.
가스로 작동하는 다리미는 촉매 팁을 사용하여 불꽃 없이 약간의 열을 가합니다.온풍 건과 연필을 사용하면 전기 다리미와 건으로는 쉽게 수행할 수 없는 부품 패키지(예: 표면 장착 장치)를 재작업할 수 있습니다.
납땜 토치는 납땜 팁이 아닌 불꽃을 사용하여 납땜을 가열합니다.납땜 횃불은 종종 부탄에[19] 의해 작동되며 매우 미세하지만 고온의 보석 작업에 적합한 매우 작은 부탄/산소 단위부터 구리 배관과 같은 훨씬 더 큰 작업에 적합한 실물 크기의 산소 연료 횃불에 이르기까지 다양한 크기로 제공됩니다.일반적인 다목적 프로판 토치는 열박리 페인트 및 해동 파이프에 사용되는 것과 동일한 종류로, 납땜 팁 부착물이 있든 없든 납땜 파이프 및 기타 상당히 큰 물체에 사용할 수 있습니다. 일반적으로 파이프는 개방된 불꽃을 직접 도포하여 토치로 납땜합니다.
납땜용 구리는 구리 헤드가 크고 손잡이가 긴 공구로 작은 직접 불꽃으로 가열하여 주석 도금강 등 판금에 열을 가하여 납땜을 하는 데 사용됩니다.전형적인 납땜 구리의 머리는 1에서 4파운드 사이입니다.헤드는 큰 열 질량을 제공하여 넓은 영역을 납땜하기에 충분한 열을 저장한 후 불 속에서 다시 가열해야 합니다. 헤드가 클수록 작업 시간이 길어집니다.공구의 구리 표면은 사용 중에 지속적으로 세척하고 다시 주석 처리해야 합니다.역사적으로 납땜 구리는 자동차 차체 작업에 사용되는 표준 도구였지만, 차체 납땜은 기계적 연결을 위한 스폿 용접과 윤곽 처리를 위한 비금속 충전재로 대부분 대체되었습니다.
제2차 세계대전 동안 그리고 그 후 얼마 동안 SOE군은 소규모 폭약식 자가 납땜 접합부를 사용하여 원격 폭파 및 파괴 활동용 폭발물 연결 장치를 만들었습니다.이것들은 납땜으로 부분적으로 채워진 작은 구리 튜브와 튜브 주위를 감싼 느리게 연소되는 폭약 조성물로 구성되었습니다.접합할 와이어를 튜브에 삽입하고 점화용 화합물의 작은 방울을 성냥처럼 쳐서 폭약을 점화하고 솔더를 녹여서 [citation needed]접합부를 만들 수 있을 정도로 오랫동안 튜브를 가열할 수 있었습니다.
레이저 납땜
레이저 솔더링(Laser soldering)은 30~50W 레이저를 사용하여 전기적 연결 조인트를 녹이고 납땜하는 방법입니다.반도체 접합에 기반한 다이오드 레이저 시스템이 [20]이 목적을 위해 사용됩니다.수잔 제니쉬는 [21]1980년에 레이저 납땜 특허를 받았습니다.
파장은 일반적으로 808nm ~ 980nm입니다.빔은 광섬유를 통해 작업물로 전달되며, 섬유 직경은 800 ㎛ 이하입니다.섬유의 끝에서 나온 빔은 빠르게 발산되기 때문에 렌즈를 사용하여 적절한 작업 거리에서 작업물에 적합한 스폿 크기를 만듭니다.와이어 피더는 [22]솔더를 공급하기 위해 사용됩니다.
납-주석 및 은-주석 소재 모두 납땜이 가능합니다.합금 성분에 따라 공정 레시피가 달라집니다.납땜 프리폼을 사용하여 44핀 칩 캐리어를 보드에 납땜하는 경우, 전력 레벨은 10와트, 납땜 시간은 약 1초였습니다.낮은 출력 레벨은 불완전한 습윤과 공극의 형성을 초래할 수 있으며, 이 둘은 모두 관절을 약화시킬 수 있습니다.
광 납땜
광음향 납땜은 급속 펄스 플래시 램프에서 회로 [23]기판으로 부품을 납땜하는 광대역 광을 사용하는 비교적 새로운 프로세스입니다.에너지 소비량은 리플로우 오븐에 비해 약 85% 적은 반면 처리량은 높고 설치 공간은 적습니다.납땜할 구성 요소가 가열되고 기판이 [24]비교적 냉각된 상태로 유지된다는 점에서 광 경화와 유사합니다.이를 통해 PET, 셀룰로오스 및 [25]직물과 같은 열적으로 취약한 기판에도 SAC305와 같은 고온 솔더를 사용할 수 있습니다.전체 회로 기판을 몇 초 안에 처리할 수 있습니다.마스크를 사용하는 경우도 있지만, 등록 없이 수행할 수도 있어 매우 높은 처리율이 가능합니다.
인덕션 솔더링
인덕션 솔더링은 주변 구리 코일에 고주파 교류에 의한 인덕션 가열을 이용합니다.이로 인해 납땜되는 부품에 전류가 유도되며, 이는 주변 금속(저항 가열)에 비해 접합부의 저항이 높기 때문에 열을 발생시킵니다.이러한 구리 코일은 접합부에 더 정확하게 맞도록 형상화할 수 있습니다.충전재 금속(솔더)이 대면면 사이에 배치되고, 이 솔더는 상당히 낮은 온도에서 용융됩니다.플럭스는 유도 납땜에 일반적으로 사용됩니다.이 기술은 특히 연속적인 납땜에 적합하며, 이 경우 이러한 코일은 납땜이 필요한 실린더 또는 파이프를 감싼다.
섬유 초점 적외선 납땜
섬유 초점 적외선 납땜은 많은 적외선 소스가 섬유를 통해 유도된 다음 연결 부위가 [26][failed verification]납땜되는 단일 지점에 초점을 맞추는 기술입니다.
저항 납땜
저항 납땜은 납땜 대상 부품에 전류를 통과시킴으로써 납땜을 녹이는 데 필요한 열을 생성하는 납땜입니다.전류가 금속을 통해 전도되면 열이 발생합니다. 전류가 단면적이 작은 부분에 국한되면 전체 회로에서 발생하는 열이 단면적이 감소된 부분에 집중됩니다.가열을 수행하는 전류는 전극 또는 팁에 의해 낮은(개방 회로) 전압원(일반적으로 2~7V)에서 통전됩니다.일반적인 연결을 위한 핀셋 형태일 수도 있고, 서로 가까이 위치한 부품과 접촉할 수 있도록 특수한 형태일 수도 있습니다.
저항 납땜은 열이 요소 내에서 생성된 후 열전도 팁을 통해 접합부로 전달되는 전도 철을 사용하는 것과는 다릅니다.냉연 인두는 작업 온도에 도달하는 시간이 필요하며, 납땜 접합부 사이를 뜨겁게 유지해야 합니다.사용 중 팁이 제대로 젖지 않으면 열전달이 억제될 수 있습니다.저항 납땜 기능을 통해 강한 열이 접합부 내에서 직접적으로 그리고 엄격하게 제어되는 방식으로 빠르게 발생할 수 있습니다.이를 통해 필요한 솔더 용융 온도까지 더 빠르게 상승할 수 있으며 솔더 조인트에서 열 이동을 최소화할 수 있으므로 주변 영역의 재료 또는 부품에 대한 열 손상 가능성을 최소화할 수 있습니다.각 조인트가 만들어지는 동안에만 열이 발생하므로 저항 납땜을 통해 에너지 효율이 향상됩니다.이러한 장점 때문에 커넥터, 전선 단자와 같이 좁은 공간에서 납땜을 하는 산업과 [27]자동차 부품의 탈납과 같이 고출력이 요구되는 산업에서 저항 납땜이 일반적입니다.
저항 납땜 장비는 전도성 철과 달리 매우 높은 온도가 필요할 수 있는 어려운 납땜 및 브레이징 용도에 사용할 수 있습니다.이는 경우에 따라 화염 납땜과 유사한 저항을 제공하지만, 직접적인 접촉으로 인해 저항 열이 더 국부적으로 발생하는 반면 화염은 더 넓은 영역을 가열할 수 있습니다.
능동납땜
일반적인 납땜 철, 초음파 납땜 철 또는 특수 납땜 냄비와 활성 원소(대부분 티타늄, 지르코늄 또는 크롬)[28]를 포함하는 활성 납땜의 도움을 받는 플럭스리스 납땜.활성 요소는 기계적 활성화로 인해 사전 금속화 없이는 일반적으로 납땜이 어렵다고 여겨지는 재료의 표면과 반응합니다.활성 솔더는 산소와 친화성이 높은 희토류 원소(일반적으로 세륨 또는 란탄)를 추가함으로써 활성 원소의 과도한 산화로부터 보호될 수 있습니다.또 다른 일반적인 첨가제는 일반적으로 습윤 촉진제로 도입되는 갈륨입니다.능동적 납땜에 필요한 기계적 활성화는 브러시(예: 스테인리스 와이어 브러시 또는 강철 주걱 사용) 또는 초음파 진동(20~60kHz)을 통해 수행할 수 있습니다.능동적 납땜은 세라믹,[28] 알루미늄, 티타늄, 실리콘,[29] 흑연 및 탄소 나노튜브 기반 구조물을 450°C보다 낮은 온도에서 효과적으로 접합하거나 보호 분위기를 사용하는 것으로 나타났습니다.
파이프납땜


구리 파이프, 즉 '튜브'는 일반적으로 납땜에 의해 결합됩니다.미국의 배관 무역 상황에서 적용될 때, 납땜은 종종 땀 흘리기로 언급되고, 이렇게 만들어진 배관 연결부는 땀 흘리기로 언급됩니다.
미국 밖에서 "스웨팅"이란 평평한 금속 표면을 두 단계 공정으로 접합하는 것을 말합니다. 이 공정을 통해 솔더가 먼저 한 표면에 도포된 다음 이 첫 번째 조각을 두 번째 표면에 대해 위치시키고 둘 다 다시 가열하여 원하는 접합을 달성합니다.
구리 배관은 기존의 휴대용 납땜 철 또는 건이 제공할 수 있는 것보다 훨씬 더 빨리 열을 전달하므로, 필요한 전력을 공급하기 위해 프로판 토치가 가장 일반적으로 사용됩니다. 대규모 배관 크기와 MAPP 연료, 아세틸렌 연료 피팅의 경우,또는 산화제로서 대기 공기와 함께 프로필렌 연료 토치를 사용합니다. MAPP/산소 또는 아세틸렌/산소는 화염 온도가 구리의 녹는점보다 훨씬 높기 때문에 거의 사용되지 않습니다.너무 많은 열은 성질이 단단한 구리 배관의 온도를 파괴하고 솔더를 추가하기 전에 접합부의 플럭스를 연소시켜 접합부에 결함이 생길 수 있습니다.더 큰 튜브 크기의 경우 다양한 크기의 상호 교환 가능한 스월 팁이 장착된 토치를 사용하여 필요한 난방 전력을 공급합니다.숙련된 무역업자의 손에 의해 아세틸렌, MAPP 또는 프로필렌의 더 뜨거운 불꽃이 구리 템퍼링의 손상 없이 시간당 더 많은 접합을 완료할 수 있습니다.
그러나 전기 공구를 사용하여 다음과 같은 크기의 구리 파이프의 접합부를 납땜하는 것은 가능합니다.8 ~ 22 mm (3 ≥ 8 ~ 7 ≥ 8 in).예를 들어, Antex Pipe Master는 좁은 공간에서, 불꽃이 위험할 때, 또는 직접 작업하는 사용자가 사용하는 것이 좋습니다.펜치와 같은 도구는 파이프를 완전히 감싸는 가열된 장착 턱을 사용하여 접합부를 10초 [31]이내에 녹일 수 있습니다.
납땜 피팅(solder fitting) 또는 '모관 피팅(capillary fitting)'은 보통 구리 접합부에 사용됩니다.이 피팅은 매끄러운 파이프의 짧은 섹션으로, 접합 튜브의 바깥쪽을 미끄러지도록 설계되었습니다.일반적으로 사용되는 피팅에는 일자 커넥터, 감속기, 벤드 및 티가 포함됩니다.솔더 피팅에는 솔더가 포함되지 않은 '엔드 피드 피팅'과 피팅 내부의 작은 원형 오목부에 솔더 링이 있는 '솔더 링 피팅'(요크셔 피팅이라고도 함)의 두 가지 유형이 있습니다.
모든 솔더 조인트와 마찬가지로 접합되는 모든 부품은 깨끗하고 산화물이 없어야 합니다.내부 및 외부 와이어 브러시는 공통 파이프 및 피팅 크기에 사용할 수 있습니다. 에머리 천 및 와이어 울도 자주 사용되지만 금속 울 제품에는 오일이 함유되어 있어 조인트를 오염시킬 수 있으므로 권장되지 않습니다.
관련 부품의 크기와 화염의 높은 활성 및 오염 경향으로 인해 배관 플럭스는 일반적으로 전자 플럭스보다 훨씬 더 화학적으로 활성이며 종종 더 산성입니다.배관 접합부는 어떤 각도(거꾸로 되어도)로도 이루어질 수 있기 때문에 배관 플럭스는 일반적으로 액체보다 제 위치에 더 잘 유지되는 페이스트로 공식화됩니다.플럭스는 조인트의 안쪽과 바깥쪽 모든 표면에 도포됩니다.조인트가 완료된 후에는 조인트의 부식 및 고장을 방지하기 위해 플럭스 잔재물을 제거합니다.
작업의 특정 요구 사항에 따라 용융 온도가 높거나 낮아지는 등 다양한 특성을 가진 많은 배관용 솔더 제형을 사용할 수 있습니다.건축 법규는 현재 거의 보편적으로 음용수 배관에 무연 솔더를 사용해야 하지만, 기존의 주석 납 솔더는 여전히 사용할 수 있습니다. (그리고 플럭스는 음용수 용도로 승인되어야 함)연구에 따르면 납땜된 배관 파이프는 식수의 [32][33]납 수준을 높일 수 있습니다.
구리 파이프는 접합부로부터 빠르게 열을 전달하기 때문에 접합부가 잘 가열되도록 세심한 주의를 기울여야 합니다.조인트를 적절히 세척하고 플럭스 및 장착한 후, 토치 화염은 조인트의 가장 두꺼운 부분(일반적으로 내부에 파이프가 있는 피팅)에 도포되며, 솔더는 튜브와 피팅 사이의 갭에 도포됩니다.모든 부품이 가열되면 솔더가 녹아 모세관 작용에 의해 접합부로 유입됩니다.모든 부위가 젖었는지 확인하기 위해 토치를 조인트 주위로 이동시켜야 할 수도 있습니다.그러나 납땜되는 부분이 과열되지 않도록 설치자가 주의해야 합니다.튜브가 변색되기 시작하면 튜브가 과열되어 산화되기 시작하여 솔더의 흐름이 중단되고 솔더 조인트가 제대로 씰링되지 않음을 의미합니다.산화되기 전에 용융 솔더는 접합부 주위에서 토치의 열을 따릅니다.이음새가 제대로 젖으면 땜납과 열이 제거되고 이음새가 여전히 매우 뜨거울 때 보통 마른 천으로 닦습니다.이를 통해 여분의 솔더와 플럭스 잔여물을 제거한 후 냉각 및 경화됩니다.솔더 링 조인트의 경우, 피팅 가장자리 주변에 용융 솔더 링이 보일 때까지 조인트가 가열되어 냉각됩니다.
구리 배관을 연결하는 세 가지 방법 중 납땜 연결에는 가장 많은 기술이 필요하지만 몇 가지 기본 조건이 충족된다면 구리 납땜은 매우 신뢰할 수 있는 프로세스입니다.
- 튜빙 및 피팅은 금속이 벗겨지지 않도록 청소해야 합니다.
- 튜브 가열에 의해 형성되는 압력은 반드시 배출구가 있어야 합니다.
- 조인트는 건조해야 합니다(수도관을 수리할 때 어려울 수 있음).
구리는 이런 방식으로 결합된 하나의 물질일 뿐입니다.황동 피팅은 종종 밸브 또는 구리와 다른 금속 사이의 연결 피팅으로 사용됩니다.금관악기와 목관악기(색소폰, 플루트)를 만들 때 금관악기는 이런 방식으로 납땜됩니다.
와이어 브러시, 와이어 울 및 에머리 천은 연결을 위한 배관 조인트를 준비하는 데 일반적으로 사용됩니다.강모 브러시는 일반적으로 배관 페이스트 플럭스를 도포하는 데 사용됩니다.무거운 래그는 배관 이음매가 냉각 및 경화되기 전에 플럭스를 제거하는 데 일반적으로 사용됩니다.섬유 유리 브러시도 사용할 수 있습니다.
냉동 시스템과 같이 밸브에 밀접하게 연결된 납땜 파이프의 경우 내부의 고무 또는 플라스틱 구성 요소를 손상시킬 수 있는 열로부터 밸브를 보호해야 할 수 있습니다. 이 경우 밸브를 감싼 젖은 천은 종종 [citation needed]밸브를 보호하기 위해 물의 비등을 통해 충분한 열을 흡수할 수 있습니다.
동관 납땜 불량
구리 튜브를 접합할 때 조인트를 적절하게 가열하고 채우지 않으면 '공극'이 발생할 수 있습니다.이는 일반적으로 화염의 부적절한 배치로 인해 발생합니다.불꽃의 열이 피팅 컵의 뒤쪽을 향하지 않고 솔더 와이어가 불꽃의 반대 방향으로 도포되면[quantify] 솔더가 피팅의 개구부를 빠르게 채워 조인트 내부에 플럭스가 다소 갇히게 됩니다.끼인 플럭스의 기포는 공극입니다. 솔더가 피팅의 컵을 완전히 채울 수 없는 솔더 조인트 내부 영역입니다. 플럭스가 조인트 내부에서 밀봉되어 솔더가 그 공간을 차지하는 것을 방지하기 때문입니다.
스테인드글라스 납땜
역사적으로, 스테인드 글라스 납땜 팁은 구리였고, 숯을 태우는 화로에 넣어 가열되었습니다.여러 팁이 사용되었는데, 한 팁이 식으면 다시 숯의 화로에 넣고 다음 팁을 사용했습니다.
최근에는 전기로 가열된 납땜용 다리미가 사용되고 있습니다.이것들은 철 끝 안에 있는 코일이나 세라믹 발열체에 의해 가열됩니다.다양한 전력 등급을 사용할 수 있으며 온도는 전자적으로 제어할 수 있습니다.이러한 특성을 통해 팁을 변경하기 위해 작업을 중단하지 않고 더 긴 비드를 실행할 수 있습니다.전자적 용도로 설계된 납땜용 다리미는 종종 효과적이지만 때때로 무거운 구리와 스테인드 글라스 작업에 사용된 납에 비해 전력이 부족합니다.납땜성을 향상시키기 위해 사용되어 온 대표적인 플럭스 재료는 올레산입니다.
티파니 타입의 스테인드 글라스는 유리 조각의 가장자리에 동박을 붙인 후 납땜하여 만들어집니다.이 방법은 3차원 스테인드 글라스 조각을 만드는 것을 가능하게 합니다.
전자납땜
손납땜

PCB에 전자 부품을 부착하려면 플럭스를 적절히 선택하여 사용하면 납땜 시 산화를 방지하는 데 도움이 되며, 이는 습윤 및 열전달이 잘 되는 데 필수적입니다.납땜용 철 팁은 청결해야 하며 신속한 열 전달을 위해 솔더로 미리 주석 처리해야 합니다.
전자 접합부는 일반적으로 주석 처리가 완료된 표면 사이에 만들어지며 기계적 세척이 거의 필요하지 않습니다. 비록 (노후화로 인해) 산화물 패시베이션의 어두운 층을 가진 손상된 부품 리드와 구리 흔적이 선반에 약 1년 이상 보관된 새 시제품 제작 보드와 같이 기계적 세척이 필요할 수도 있습니다.
납땜을 단순화하기 위해 초보자들은 보통 납땜을 직접 철기에 바르기보다는 납땜 철과 납땜을 따로 관절에 바르는 것이 좋습니다.솔더가 충분히 도포되면 솔더 와이어를 제거합니다.표면이 충분히 가열되면 땜납이 공작물 주위를 돌게 됩니다.그런 다음 철을 접합부에서 제거합니다.
모든 금속 표면이 제대로 세척되지 않았거나("플럭스") 사용된 솔더의 용융 온도를 완전히 초과한 경우, 외관이 그렇지 않음을 시사할 수 있음에도 불구하고 신뢰할 수 없는("콜드 솔더") 접합부가 됩니다.
과도한 납땜, 소비되지 않은 플럭스 및 잔여물은 접합부 사이의 납땜 철 팁에서 닦아내기도 합니다.비트(흔히 부식을 줄이기 위해 도금된 철)의 끝은 납땜을 돕고 팁 자체의 산화 및 부식을 최소화하기 위해 뜨거울 때 땜납("주석 처리")으로 적셔집니다.
관통홀 장착 부품을 삽입한 후, 패드 반경 정도의 길이를 남기고 초과 리드를 절단합니다.
핸드 솔더링 기술은 표면 장착 칩 패키지의 미세 피치 솔더링을 위해 많은 기술을 필요로 합니다.특히 BGA(Ball Grid Array) 장치는 불가능하지는 않더라도 손으로 재작업하는 것이 어렵기로 악명이 높습니다.
결점
냉관절

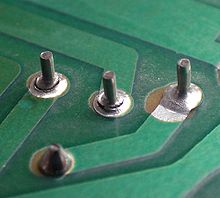
납땜 과정에서 여러 가지 문제가 발생할 수 있으며, 이로 인해 접합부가 즉시 또는 사용 후에 작동하지 않게 됩니다.
손으로 솔더링할 때 가장 일반적인 결함은 접합되는 부품이 솔더의 액체 온도를 초과하지 않아 "콜드 솔더" 접합으로 인해 발생합니다.이는 일반적으로 부품 자체가 아닌 납땜을 직접 가열하는 데 사용되는 납땜 철의 결과입니다.적절히 처리되면, 철은 연결될 부품을 가열하고, 이는 다시 솔더를 녹여서, 완전한 습윤을 위해 접합된 부품에 충분한 열을 보장합니다.플럭스 코어가 내장된 솔더 와이어를 사용하는 경우, 솔더를 먼저 가열하면 표면을 세척하기 전에 플럭스가 증발될 수 있습니다.
냉연 접합부는 전혀 전도되지 않거나 간헐적으로만 전도될 수 있습니다.냉연 접합부는 대량 생산 시에도 발생하며, 테스트를 통과하는 장비의 일반적인 원인이지만 작동 후 몇 년이 지나면 오작동합니다.
건관절
냉각 솔더를 이동시킬 때 "드라이 조인트"가 발생합니다.비유테틱 솔더 합금은 플라스틱 범위가 작기 때문에, 솔더가 액체 온도와 고체 온도를 통해 냉각될 때까지 조인트를 이동시키지 말아야 합니다.관절에서 납땜철을 제거하면 관절이 움직이기 때문에 건조한 관절이 자주 발생합니다.그들은 기계적으로 약하고 전기적으로 불량한 도체입니다.
부품 과열 방지
손 솔더링의 경우, 완성할 조인트 크기에 적합한 열을 제공하기 위해 열원 공구를 선택합니다.100와트의 납땜 다리미는 인쇄 회로 기판(PCB)에 너무 많은 열을 공급할 수 있는 반면, 25와트의 다리미는 대형 전기 커넥터에 충분한 열을 공급하지 못할 수 있습니다.
온도가 너무 높은 공구를 사용하면 민감한 구성 요소가 손상될 수 있지만, 너무 시원하거나 전력이 부족한 공구를 사용하여 장시간 가열할 경우 열 손상이 발생할 수도 있습니다.PCB를 과도하게 가열하면 층간 박리가 발생할 수 있습니다. 구리 트레이스가 실제로 기판을 들어올릴 수 있으며, 특히 관통 구멍 도금이 없는 편면 PCB에서는 더욱 그렇습니다.
손으로 솔더링하는 동안 열에 민감한 부품의 리드에 악어 클립과 같은 히트 싱크를 사용하여 부품으로의 열 전달을 줄이고 손상을 방지할 수 있습니다.이는 특히 게르마늄 부품에 적용할 수 있습니다.
히트 싱크는 열을 흡수하고 방출함으로써 부품과 공기 사이의 열 저항을 감소시켜 부품 본체의 온도를 제한합니다.한편, 리드의 열저항은 납땜되는 리드의 부분과 부품 본체 사이의 온도차를 유지합니다.따라서 부품 본체가 냉각된 상태로 유지되는 동안 납은 솔더를 녹일 수 있을 정도로 뜨거워집니다.히트 싱크는 더 많은 열을 사용하여 조인트를 완성하는 것을 의미합니다. 히트 싱크에 의해 흡수된 열은 작업물을 가열하지 않기 때문입니다.
작동 중에 많은 양의 열을 방출하는 구성 요소는 PCB 과열을 방지하기 위해 PCB 위로 올라가는 경우가 있습니다.플라스틱 또는 금속 마운팅 클립 또는 홀더는 열 방출을 돕고 조인트 응력을 줄이기 위해 대형 장치와 함께 사용할 수 있습니다.
접합부 육안검사
육안으로 검사할 때 양호한 솔더 조인트가 매끄럽고 밝고 반짝이며 납땜된 와이어의 윤곽이 명확하게 보입니다.일반적으로 보기 좋은 납땜 조인트가 좋은 조인트입니다.
무광 회색 표면은 납땜 중에 이동한 관절의 좋은 지표입니다.건조한 관절은 관절을 만든 직후에 특징적으로 둔탁하거나 알갱이 모양으로 되어 있습니다.이와 같은 외관은 액상 솔더의 결정화에 의한 것입니다.솔더가 너무 적으면 조인트가 건조하고 신뢰성이 떨어집니다.
콜드 솔더 접합부는 둔하며 때로는 금이 가거나 펑크가 나기도 합니다.접합부에 번들거리는 납땜의 덩어리나 공이 있는 경우 금속이 제대로 젖지 않은 것입니다.너무 많은 납땜(초보자에게 익숙한 납땜 방울)은 반드시 소리가 나지 않는 것은 아니지만, 습기가 부족하다는 것을 의미하는 경향이 있습니다.
오목한 살코기가 이상적입니다.양호한 조인트의 솔더와 가공물 사이의 경계는 낮은 각도를 가질 것입니다.이는 납땜의 사용을 최소화하고, 따라서 열에 민감한 부품의 가열을 최소화할 수 있음을 나타냅니다.조인트가 좋을 수도 있지만 불필요한 솔더를 다량으로 사용할 경우 과도한 가열이 필요한 것은 분명합니다.
무연 솔더 제형은 접합부가 좋아도 표면이 칙칙하게 냉각될 수 있습니다.땜납은 녹은 상태에서 반짝반짝 빛나고, 냉각 중에 흐트러지지 않았는데도 응고되면서 갑자기 헤징됩니다.
플럭스 사용 및 잔사
플럭스를 잘못 선택하거나 적용할 경우 조인트 고장이 발생할 수 있습니다.플럭스가 없으면 조인트가 깨끗하지 않거나 산화되어 조인트가 손상될 수 있습니다.
전자 작업의 경우 플럭스 코어 솔더 와이어가 일반적으로 사용되지만 플럭스 펜에서 추가 플럭스를 사용하거나 주사기와 같은 바늘이 있는 작은 병에서 분사할 수도 있습니다.
일부 플럭스는 냉각 시 안정적이고 비활성화되도록 설계되어 있으며, 원하는 경우 세척할 필요가 없습니다.이러한 플럭스를 사용할 경우, 단순히 심미성의 문제일 수도 있고 의료 기기, 군사 및 항공 우주와 같은 특수한 '임무상 중요한' 용도에서 관절의 육안 검사를 용이하게 할 수도 있습니다.위성의 경우, 이것은 또한 무게를 약간 줄이겠지만 유용하게 사용될 것입니다.습도가 높은 경우 부식되지 않는 플럭스라도 약간 활성 상태를 유지할 수 있으므로 플럭스를 제거하여 시간 경과에 따른 부식을 줄일 수 있습니다.
일부 플럭스는 부식성이 있으며 납땜 후 플럭스 잔여물을 제거해야 합니다.제대로 세척하지 않으면 플럭스가 조인트 또는 PCB를 부식시킬 수 있습니다.물, 알코올, 아세톤 또는 플럭스와 관련된 기타 용매는 면봉 또는 강모 브러시와 함께 일반적으로 사용됩니다.
일부 용도에서는 PCB를 보호하기 위해 래커와 같은 보호 재료 형태로 코팅하고 솔더 접합부를 환경으로부터 노출시킬 수도 있습니다.
디솔더링 및 재설정

사용된 땜납은 용해된 염기 금속의 일부를 포함하고 있어 새로운 접합부를 만들 때 재사용하기에 부적합합니다.기본 금속에 대한 솔더의 용량에 도달하면 더 이상 기본 금속과 적절하게 결합하지 못하고, 일반적으로 결정형 외관을 가진 부서지기 쉬운 콜드 솔더 조인트가 발생합니다.
솔더링 전에 이음매에서 솔더링을 제거하는 것이 좋습니다. 솔더링 땋은 부분(또는 심지) 또는 진공 솔더링 장비(솔더링 빨판)를 사용할 수 있습니다.납땜용 윅에는 구리 트레이스와 존재하는 모든 장치 리드에서 산화를 제거하는 플럭스가 다량 포함되어 있습니다.이렇게 하면 밝고 반짝이는 깨끗한 접합부가 다시 납땜됩니다.
솔더의 녹는점이 낮아 기본 금속으로부터 멀어질 수 있음을 의미하며, 대부분 그대로 남아 있지만, 외부 층은 솔더로 "두꺼운" 상태가 됩니다.연마 공정이나 화학 공정으로 쉽게 제거할 수 있는 플럭스가 남아 있습니다.이 주석 처리된 층은 솔더가 새로운 접합부로 흘러가도록 하여 새로운 접합부를 생성할 뿐만 아니라 새로운 솔더가 매우 빠르고 쉽게 흘러가게 할 것입니다.
웨이브 솔더링 및 리플로우 솔더링
현재 양산형 인쇄회로기판(PCB)은 대부분 웨이브 납땜 또는 리플로우 납땜이 주를 이루고 있지만, 생산용 전자제품의 핸드 납땜도 여전히 널리 사용되고 있습니다.
웨이브 솔더링에서는 부품이 준비(트림 또는 수정)되어 PCB에 설치됩니다.때때로 움직임을 방지하기 위해 일시적으로 접착제의 작은 댑(dab)으로 고정되거나 고정 장치로 고정된 다음 어셈블리를 대량 용기에 흐르는 솔더 위로 보냅니다.이 땜납 흐름은 정상파를 생성하도록 강요되어 PCB 전체가 땜납에 잠기지 않고 그냥 만져집니다.그 결과 땜납은 핀과 패드 위에 머물지만 PCB 자체에는 머물지 않습니다.
리플로우 솔더링(Reflow soldering)은 납땜 페이스트(미리 합금된 납땜 분말과 땅콩 버터와 같은[7] 일관성을 가진 플럭스 차량의 혼합물)를 사용하여 부품을 부착 패드에 부착한 후 적외선 램프, 열풍 연필 또는 더 일반적으로,그것을 조심스럽게 조절된 오븐에 통과시킴으로써.
서로 다른 구성요소들은 서로 다른 기술에 의해 가장 잘 조립될 수 있기 때문에, 주어진 PCB에 대해 두 개 이상의 공정을 사용하는 것이 일반적입니다.예를 들어, 표면 장착 부품은 리플로우 솔더링을 먼저 수행하고, 관통 홀 장착 부품에 대한 웨이브 솔더링 공정은 다음에 수행하고, 부피가 큰 부품은 손으로 솔더링을 수행하는 경우가 마지막에 수행할 수 있습니다.
핫바 리플로우
핫바 리플로우(hot-bar reflow)는 솔더를 녹이기에 충분한 온도로 가열하는 선택적 솔더링 공정입니다.
전체 프로세스(보통 15초)를 통해 압력을 가하여 냉각 중에도 구성 요소가 제자리에 있도록 합니다.발열체는 각 연결부마다 가열 및 냉각됩니다.발열체에는 최대 4000W를 사용할 수 있어 빠른 납땜이 가능하며 높은 [34]에너지를 필요로 하는 연결부로 좋은 결과를 얻을 수 있습니다.
환경규제와 RoHS
많은 국가에서 환경 관련 법규를 제정함에 따라 납땜 및 플럭스의 제형이 모두 변경되었습니다.
유럽 공동체의 RoHS 지침에 따라 2006년 7월 1일까지 납이 없는 새로운 전자 회로 기판이 많이 필요하게 되었고, 대부분은 소비재 산업에서, 일부에서는 납이 없는 경우도 있었습니다.일본에서는 [35]납이 함유된 제품의 재활용에 추가적인 비용이 들기 때문에 제조업체의 법 제정 이전에 납이 단계적으로 폐기되었습니다.
수용성 비로신 기반 플럭스는 납땜된 보드를 물 또는 수성 세정제로 세정할 수 있도록 1980년대 이후 점점 더 많이 사용되고 있습니다.이를 통해 생산 환경 및 공장 유출물로부터 유해 용매를 제거할 수 있습니다.
납이 없어도 납땜은 인체에 유해하거나 독성이 있는 연기를 방출할 수 있습니다.외부를 환기하거나 [36]공기를 여과하여 작업 공간의 매연을 제거할 수 있는 장치를 사용하는 것이 좋습니다.
무연
무연 납땜은 납/주석 납땜보다 더 높은 납땜 온도를 요구합니다.SnPb 63/37 공융 땜납은 183°C에서 녹습니다.SAC 무연 솔더는 217~220℃에서 용융됩니다.그럼에도 불구하고, 이 노력으로 인해 많은 새로운 기술적 과제들이 발생했습니다.주석계 솔더 합금의 융점을 감소시키기 위해 다양한 새로운 합금들이 연구되어야 했는데, 융점을 감소시키고 다른 특성을 조절하기 위해 구리, 은, 비스무트의 첨가제들이 대표적인 미량 첨가제로 사용되었습니다.또한 주석은 보다 부식성이 강한 금속이므로 결국 솔더[clarification needed] [35]배스의 실패로 이어질 수 있습니다.
무연 구조는 부품, 핀, 커넥터로도 확장되었습니다.대부분의 핀은 구리 프레임과 납, 주석, 금 또는 다른 마감재를 사용했습니다.주석 마감은 무연 마감 중 가장 인기가 많습니다.그러나, 이는 주석 수염을 어떻게 처리할 것인가에 대한 문제를 야기합니다.현재의 움직임은 전자 산업을 1960년대에 납을 추가함으로써 해결된 문제로 되돌립니다.JEDEC는 무연 전자 제조업체가 용도에 따라 수염에 대해 취할 조치를 결정할 수 있도록 분류 시스템을 만들었습니다.
참고 항목
참고문헌
- ^ Brady, George; et al. (1996). Materials Handbook. McGraw Hill. pp. 768–70. ISBN 978-0-07-007084-4.
- ^ "A History of Welding". weldinghistory.org. Archived from the original on 25 April 2012. Retrieved 2 May 2018.
- ^ "Lead Free Solders". hybridmetals.com. Retrieved 2021-11-23.
- ^ White, Kent. "Brazing versus Soldering". TM Technologies, Tools & Methods for Better Metalworking. Archived from the original on 23 June 2017. Retrieved 2 May 2018.
- ^ Kapp Alloy & Wire, Inc. "Products". Kapp Alloy & Wire, Inc. Archived from the original on 16 July 2013. Retrieved 5 March 2013.
- ^ AWS A3.0:2001, 접착제 접합, 브레이징, 솔더링, 열절단 및 용사에 대한 용어를 포함하는 표준 용접 용어 및 정의, 미국 용접 협회(2001), 페이지 118. ISBN 0-87171-624-0
- ^ a b c "Indium Corporation Global Solder Supplier Electronics Assembly Materials". Indium Corporation. Archived from the original on 25 June 2012. Retrieved 2 May 2018.
- ^ Rahn, Armin (1993). "1.1 Introduction". The Basics of Soldering. John Wiley & Sons. ISBN 978-0-471-58471-1.
- ^ "When Brazing Beats Welding". Machine Design. Retrieved 2020-09-02.
- ^ 고온 재료에서 금-니켈 합금 납땜 접합부의 특성, Gold Bulletin, June 1974, 7권, 2호, pp 42-49; Jakob Colbus and Karl Friedrich Zimmermann; https://doi.org/10.1007/BF03215037
- ^ a b Alumaloy 2009-03-05 Wayback Machine에서 보관, 2009-04-03 액세스
- ^ a b Alumiweld FAQ 2009-05-01 Wayback 기계에서 보관, 2009-04-03 액세스
- ^ MIL-R-4208 아카이브 2013-02-04 오늘, 2009-04-03 액세스
- ^ 알라딘 3-in-1 Wayback Machine에서 2009-02-07 보관, 2009-04-03 액세스
- ^ HTS-2000 Wayback Machine에서 2009-02-13 보관, 2009-03-09 액세스
- ^ "Flux and epoxy products made by Indium Corporation". Indium Corporation. Archived from the original on 20 August 2012. Retrieved 2 May 2018.
- ^ "An Investigation of the Chemistry of Citric Acid in Military Soldering Applications" (PDF). 1995-06-19. Archived (PDF) from the original on March 15, 2020.
- ^ IPC-A-610 개정판 E섹션 10.6.4
- ^ "Soldering Training Equipment - Tooling U-SME". www.toolingu.com. Archived from the original on 3 December 2015. Retrieved 2 May 2018.
- ^ 0204 www.coherent.com
- ^ "SWE Women - Jenniches". Society of Women Engineers. Archived from the original on 20 May 2014. Retrieved 20 May 2014.
- ^ 070927 ma-info.de
- ^ van den Ende, D. A.; Hendriks, R.; Cauchois, R.; Groen, W. A. (November 2014). "Large area photonic flash soldering of thin chips on flex foils for flexible electronic systems: In situ temperature measurements and thermal modelling". Electronic Materials Letters. 10 (6): 1175–1183. doi:10.1007/s13391-014-4222-3. ISSN 1738-8090. S2CID 138511242.
- ^ Ho, Ming-jaan; Li, Yanlu; Liu, Likun; Li, Yang; Gao, Chunlan (May 2021). "10‐2: Study of an Ultra‐fast Photonic Soldering Technology without Thermal Damage in Display Module Package". SID Symposium Digest of Technical Papers. 52 (1): 115–118. doi:10.1002/sdtp.14624. ISSN 0097-966X. S2CID 238032976.
- ^ Ghosh, Rudy; Akhavan, Vahid; Chou, Harry; Turkani, Vikram; Farnsworth, Stan (February 2021). "40.1: Invited Paper: Use of flash lamps to achieve non‐equilibrium soldering and assembly using conventional solder alloys". SID Symposium Digest of Technical Papers. 52 (S1): 275. doi:10.1002/sdtp.14457. ISSN 0097-966X. S2CID 234069100.
- ^ 070927 vincenc.com.tw (기술로 언급)
- ^ Alan Sherry (2 May 2022). "Why Resistance Soldering Instead of Conductive Soldering?". Stellar Technical Products.
- ^ a b M. Provazník (Jul 2012). "Study of Active Soldering of Al2O3 Sputtering Targets on Copper Substrates" (PDF). World Congress on Engineering. 3. ISSN 2078-0966. Archived (PDF) from the original on 2016-07-01.
- ^ C. Peng (Sep 2010). "Die bonding of silicon and other materials with active solder". 2010 11th International Conference on Electronic Packaging Technology & High Density Packaging. Vol. 61. pp. 1736–1739. doi:10.1109/ICEPT.2010.5582418. ISBN 978-1-4244-8140-8. ISSN 0569-5503. S2CID 13045321.
- ^ M. Burda; et al. (Aug 2015). "Soldering of carbon materials using transition metal rich alloys". ACS Nano. 9 (8): 8099–107. doi:10.1021/acsnano.5b02176. PMID 26256042.
- ^ "Pipemaster Soldering Tool". Smart Plumbing Products. Smart Contractor Products. Archived from the original on 2014-05-21. Retrieved 2014-05-20.
- ^ "Fluxes and solders". Archived from the original on 2009-02-18. Retrieved 2009-09-16.
- ^ "Lead Poisoning - Ask Dr Sears". askdrsears.com. Archived from the original on 10 November 2009. Retrieved 2 May 2018.
- ^ "Unitek Eapro: Electronic Assembly Products". Archived from the original on 2008-05-06.
- ^ a b 납 없는 납땜의 사실과 허구 www.dkmetals.co.uk 의 Wayback Machine에서 2011-03-11 보관
- ^ "The Hazards of Solder Fumes - Sentry Air Systems". www.sentryair.com. Archived from the original on 25 October 2016. Retrieved 2 May 2018.
외부 링크

