검 만들기
Sword making역사적으로 칼을 만드는 것은 블레이드미스 또는 칼잡이라고 불리는 전문 기술자 또는 금속 노동자들의 작업이었다. 칼은 수세기 동안 다양한 도구와 기술로 다른 재료로 만들어졌다. 검의 평가 기준은 많지만 일반적으로 네 가지 핵심 기준은 경도, 강도, 유연성, 균형이다. 초기 검들은 구리로[citation needed] 만들어졌고, 구리는 쉽게 구부러진다. 청동검은 더 강했다; 합금 속의 주석 양을 변화시킴으로써, 대장장이는 전투 서비스의 요구에 맞추기 위해 검의 다양한 부분을 더 단단하게 또는 더 단단하게 만들 수 있었다. 로마 글래디우스는 강철의 꽃으로 만들어진 검의 초기 예였다.
좋은 칼은 길이가 18인치(46cm)에서 36인치(91cm) 이상일 정도로 충분히 단단해야 한다. 동시에 길이와 함께 거의 어느 지점에서나 엄청난 충격을 흡수할 수 있을 정도로 튼튼하고 유연해야 하며, 균열이나 파손이 없어야 한다. 마지막으로 길이를 따라 균형을 맞춰야 효과적으로 휘두를 수 있다.
청동검
청동제품은 일반적으로 주조된 것이지 위조된 것이 아니다. 2차 작업에는 러프캐스트, 연마 및 장식 요소 적용에서 재료를 제거하는 작업이 포함된다. 어떤 중국 칼은 가장자리에 고금니를 사용했는데, 가장자리는 단단하고 날카로운 가장자리를 오래 유지하지만 칼날 코어에 사용되는 부드럽고 낮은 주금 합금보다 더 깨지기 쉽다. 주석 함량이 낮은 청동 합금은 더 단단하거나 파쇄에 더 강하다.
일본가타나
단조
일본의 대장장이들은 다른 많은 사람들과 비슷하게, 석탄(탄소)과 함께 가열된 철모래(황과 인이 거의 없이)가 타마하가네라고 부르는 강철을 만들었다는 것을 발견했다. 이를 통해 칼은 날카롭게 날을 세울 수 있는 힘과 능력을 가질 수 있을 뿐만 아니라, 스트레스를 받으면 칼이 구부러지기보다는 구부러지는 경향이 있다. 이 과정은 철과 탄소의 결합에서 시작되는데, 철모래를 전통 용광로인 타타라에서 섭씨 1200~1500도까지 72시간 동안 가열하는 것이다. 그런 다음 타마하간은 식히고 제련소는 검술사에게 보낼 가장 좋은 조각을 선택한다.
칼스미스미스
검술사는 타마하간 너겟을 잡아 한 덩어리로 만든다. 이 블록은 형성 과정에서 섭씨 900도 안팎까지 가열된다. 불 속에서 꺼내어 더 얇은 블록으로 두들겨 만든 블록은 중앙에 도끼로 점수를 매기고 위로 접혀 다시 두껍게 만든다. 그리고 나서 그 블록은 다시 불 속에 놓여진다. 강철은 가로 또는 세로 접을 수 있다. 종종 양쪽 접는 방향은 원하는 곡물 패턴을 생성하기 위해 사용된다. 시타키타에라고 불리는 이 과정은 8번에서 무려 16번까지 반복된다. 20번 접은 후에는 탄소 함량에서 너무 많은 확산이 일어나는데, 이 점에서 강철은 거의 균일하게 되며, 접는 행위는 더 이상 강철에 아무런 이점도 주지 않는다.[1]
도입되는 탄소의 양에 따라 이 과정은 하가네라고 불리는 가장자리에 매우 단단한 강철을 형성하거나, 옆면과 뒷면에 자주 사용되는 가와가네라고 하는 약간 덜 단단하게 굳는 스프링 강철을 형성한다. 검이 일단 검술사가 원하는 모양을 잡으면 검술사는 츠치오키라고 하는 검의 척추를 점토하여 다시 한 번 데우곤 했다. 일단 검이 빨갛게 달아오르자 검술사는 새로 만든 검을 받아 칼날을 굳히면서 물에 담그었다. 그리고 나서 그는 그것을 폴리셔와 피니셔에게 넘겨주곤 했다.
폴리셔와 피니셔
일단 칼날을 열처리하고 나면, 칼은 일반적으로 다른 종류의 암석인 연마재로 점차적으로 더 미세하게 갈리게 된다. 오늘날 몇 몇 개의 갈고 있는 바위들은 수천 달러에 이를 수 있다. 그들은 원하는 마무리가 될 때까지 칼을 갈고 갈았다. 이 과정은 길고 지루하지만, 훌륭한 물갈이꾼은 검술가에게 큰 가치를 지녔고 종종 좋은 보수를 받았다. 칼을 갈고 나면 미세한 끝이 날카로워질 수 있었다. 칼의 날카로움, 그리고 그 가장자리를 유지하는 능력은 칼의 가장자리의 각도와 칼의 몸 넓이를 바탕으로 한다. 그것이 가장자리를 얼마나 오래 잡아줄 수 있는가는 또한 사용되는 재료에 달려 있다.
형성
칼은 다양한 금속공법으로 모양을 만들 수 있다. 어떤 시대와 장소에서는 한 가지 기법이 독점적으로 사용되었고, 어떤 기법에서는 여러 가지 기법이 복합적으로 사용되었다. 주요 기술은 위조와 재고 제거다.
단조는 열을 이용하여 물질을 유유상종 상태로 만든다. 그런 다음 재료는 모양을 내기 위해 망치로 두들겨 만들며, 일반적으로 해머와 앤빌을 특수 세트와 풀러 공구와 함께 사용한다. 검 제작에는 다양한 위조 기법이 있고 그것에는 많은 변화가 있다.
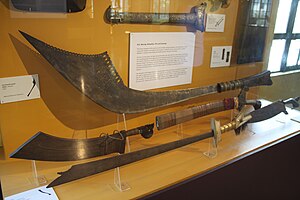
육수 제거는 완성된 칼보다 모든 차원이 큰 준비된 칼에서 다듬고 갈고 자르는 방식으로 칼 모양을 만든다. 이 기술은 수세기 동안 사용 가능했지만, 원료를 낭비하기 때문에 19세기나 20세기까지 칼을 만드는 데 널리 사용되지 않았다. 철과 철이 풍부한 곳에서는 시간이 적게 소요되기 때문에 이 방법을 자주 사용한다. 철과 철강이 더 희귀하고 가치 있는 재고 제거가 마무리 공정의 일부분 외에는 사용되지 않았던 장소와 시대.
대부분의 기법에서, 일반적으로 철이나 강철 같은 기본 재료는 바나 빌렛으로 먼저 형성된다. 이 단계에서 여러 금속을 사용할 경우 용접으로 결합하여 빌렛을 형성한다. 특히 중국, 한국, 일본의 전통적인 접힌 철골날개 등 일부 기법에서는 빌렛을 그 자체로 끌어당기고, 접고 용접하여 다른 유형의 강철 층을 만들 수도 있다. 다른 더 긴 막대 또는 강철과 철봉은 가장자리에서 가장자리로 용접되어 강철과 가장자리의 내부에 부드러운 철을 배치하는 기본 빌렛을 만들 수 있다. 빌렛이 생성되면 더 멀리 당겨지며, 일반적으로 가장자리와 지점에 테이퍼링한다. 풀레이팅 기법은 칼날 길이를 따라 능선이나 능선을 만드는 데 사용될 수 있다. 단일이든 다중이든, 블레이드의 질량에 비례하여 더 큰 구조 강도를 제공하는 능선의 주된 목적이다.
조립하는 동안, 금속은 단조 및 차등 가열로부터 쌓인 스트레스를 해소하고 금속을 철하거나, 새기거나 광내기 쉽게 하기 위해 분쇄될 수 있다.
열처리
공작물 형성이 끝나면 정상화된다. 그런 다음 칼날을 신중하고 고르게 가열한 후 천천히 식힌다. 정상화의 포인트는 칼날을 만드는 동안 칼날의 몸 안에 쌓였을 수 있는 스트레스를 제거하는 것이다. 단조 공정 동안, 칼날을 가열하고 차등적으로 냉각시켜 스트레스를 유발할 수 있으며, 어떤 부분은 다른 부분보다 더 많이 해머링될 수 있으며, 어떤 부분은 단단해질 정도로 해머링할 수 있다. 이러한 응력이 칼날에 남아 있을 경우 마감에 영향을 미칠 수 있으며 칼날을 가열 처리해야 할 때가 되면 경화와 담금질이 균일하지 않을 수 있다. 잠재적으로 충분한 스트레스는 칼날이 약하고, 충분한 스트레스로 고장날 수 있을 정도로 약할 수 있다.
검을 조작하는 마지막 과정 중 하나는 검기를 진정시키고 다듬는 것이다. 금속을 수축시키면 금속이 단단해져서 가장자리를 더 오래 잡지만 이것은 또한 금속을 매우 깨지기 쉽다. 약간의 연성과 내구성을 회복하기 위해 검을 강화한다. 칼의 경우 길이 때문에 칼날을 완만하고 고르게 들이지 않으면 칼날을 구부리거나 휘게 할 수 있기 때문에 도전은 더 크다.
칼은 또한 칼날과 같은 어떤 부분이 신체보다 단단하도록 차등적으로 굳어질 수 있다.
마무리
마무리 작업에는 자루, 가드 및 피복의 광택, 장식, 제작 및 조립이 포함된다.
검술사는 칼날 자체의 상태에 가장 신경을 쓰며 아마도 칼날을 장식하고 경비원과 안마를 준비했을 것이다. 다른 장인들은 자루, 칼집 및 기타 가구를 만드는 작업과 어떤 훌륭한 장식에도 관여할 것이다.
현대 검 만들기
칼은 여전히 현대 장인들이 만들고 있다. 어떤 사람들은 전통적인 방법을 추구하는 반면, 어떤 사람들은 현대적인 도구, 기술, 재료들을 공예에 적용한다. 상업적으로 구할 수 있는 대부분의 검들은 손으로 위조하는 것보다 더 큰 이익과 적은 시간을 가져오기 때문에 현대적인 도구와 재료로 만들어졌다. 상업적으로 구할 수 있는 대부분의 검들은 육수 제거에 의해 제조되었다.
참고 항목
참조
- ^ 시릴 스미스의 금속공학 역사 - MIT 프레스 1960 페이지 53-54
외부 링크
![]() | 위키북스에는 다음과 같은 주제의 책이 있다:검구축 |
- Anvilfire.com 무기고 기사: 이 페이지의 검 만들기 링크에 관한 몇 가지 좋은 기사.
- 칼 제작과 같은 고대 예술: 우월한 검의 신화를 없앨 수 있도록 돕는다.